Preventative Maintenance 101: A Proactive Approach to Safety and Efficiency
What if we told you that most equipment failures are entirely avoidable? That downtime, costly repairs, and safety hazards are not an inevitable part of running lifting equipment—but a consequence of neglect?
Too many businesses operate in a state of crisis, waiting for something to break before they fix it. That’s like driving a car with no oil change and hoping the engine won’t seize.
It’s reckless.
It’s expensive.
And it’s unnecessary.
Preventative maintenance is the secret weapon of the smartest operations. It’s how industry leaders maximize uptime, reduce costs, and ensure safety. And yet, so many companies still treat maintenance as an afterthought.
If you care about your bottom line, your people, and your reputation, then preventative maintenance should be a non-negotiable part of your operations.
Here’s why…

The Real Cost of Doing Nothing
Neglect is expensive. A single equipment failure can set off a domino effect—unplanned downtime, missed deadlines, frustrated customers, and emergency repair costs that far exceed the price of routine maintenance.
A study by the U.S. Department of Energy found that preventative maintenance can reduce equipment breakdowns by up to 70% and lower maintenance costs by 25%.
Let’s break that down.
– Downtime costs you money. Every minute your lifting equipment is offline, you’re bleeding revenue.
– Emergency repairs are expensive. Last-minute fixes often come with premium service fees and rush-order parts.
– Unplanned failures put safety at risk. Malfunctioning equipment is an accident waiting to happen.
Would you rather pay a small, predictable cost for regular maintenance—or risk a major financial disaster when something fails unexpectedly?
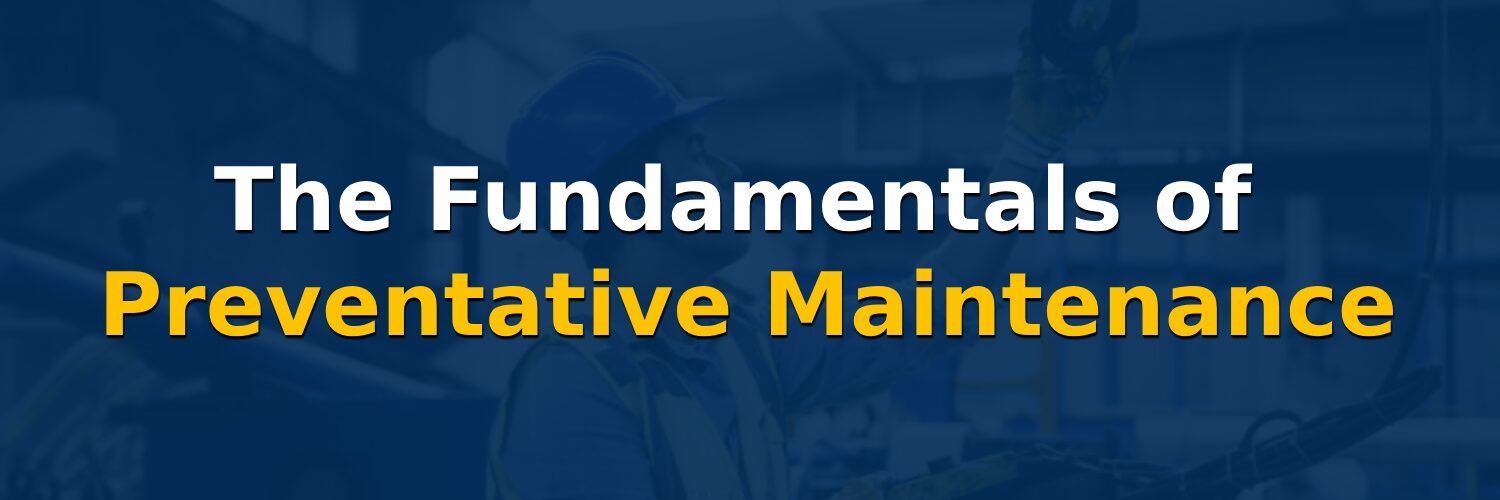
1. Regular Inspections
Your equipment speaks. It shows signs of wear, strain, and inefficiency long before it fails. Routine inspections allow you to catch minor issues before they escalate.
2. Scheduled Servicing
Think of your equipment like an athlete. Without regular conditioning, it won’t perform at its best. Scheduled servicing keeps machinery operating efficiently and extends its lifespan.
3. Lubrication and Component Replacements
Neglecting lubrication is like running a marathon without water—you won’t get far. Bearings, gears, and moving parts require proper lubrication to prevent friction, overheating, and wear.
4. Operator Training
Even the best maintenance program won’t work if your team misuses equipment. Proper training ensures that operators handle machinery correctly, reducing the risk of premature wear and tear.
5. Data-Driven Monitoring
Today’s smart technology allows for real-time monitoring of equipment performance. Sensors can detect temperature changes, vibration anomalies, and other early warning signs—allowing you to act before failure occurs.
The ROI of Preventative Maintenance
Some companies hesitate to invest in maintenance because they see it as an expense. That’s a mistake. Preventative maintenance isn’t a cost—it’s an investment with guaranteed returns.
Here’s what you gain:
✅ Increased Equipment Lifespan – Well-maintained equipment lasts longer, delaying costly replacements.
✅ Lower Repair Costs – Fixing small issues early prevents major, expensive breakdowns.
✅ Fewer Disruptions – Planned maintenance is far less disruptive than unexpected failures.
✅ Improved Safety – A proactive approach reduces workplace accidents and liability risks.
✅ Higher Productivity – Reliable equipment means fewer interruptions, leading to smoother operations.
Smart businesses don’t gamble on failure. They prevent it.
Final Thoughts: Prevention is Power
If you’re still waiting for your equipment to break before you fix it, you’re already losing.
The companies that thrive are the ones that understand this simple truth: preventative maintenance isn’t optional—it’s essential.
So, what will it be?
A proactive approach that keeps your equipment running at peak performance—or the expensive, stress-filled cycle of reactive repairs?
At Hoistech, we specialize in keeping your lifting equipment in top condition. We take all the guesswork and headache out of building a maintenance program that saves you time, money, and headaches.
The choice is yours. But remember—prevention is always cheaper than repair.